Rotational molding, commonly called Custom Rotational Molding, is just a specific plastic building process that's obtained increasing recognition in a wide range of industries. Known for making worthless, smooth, and durable pieces, rotomolding is employed for from storage tanks and outside furniture to industrial parts and automotive parts. With its unique advantages in flexibility, cost-efficiency, and product power, rotomolding has changed into a respected manufacturing technique for equally standard and custom applications.
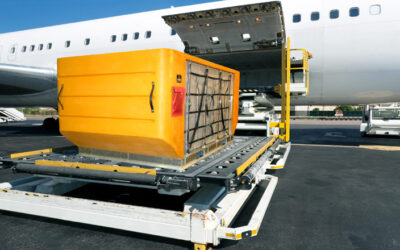
In the middle of rotomolding's appeal is their power to produce highly sturdy, stress-free components. Unlike different molding processes that use pressure during shaping, rotomolding relies on a gradual, turning mold hot in a oven. The plastic material slowly touches and coats the interior of the shape equally, producing a one-piece product without seams or weld lines. This uniform wall depth decreases weak points, making the last item more tolerant to breaking, influence, and environmental stress.
One of the most substantial advantages of rotomolding is its style versatility. The method provides for complicated patterns, multiple wall thicknesses, and inner cavities—all without the need for complex tooling or secondary assembly. Manufacturers can integrate characteristics such as threads, undercuts, and custom finishes directly into the mold. That style freedom makes rotomolding suitable for prototypes, custom styles, and low- to medium-volume generation where flexibility is key.
Cost-efficiency is still another major advantage. Tooling for rotomolding is usually less costly than that for procedure or hit molding, rendering it an even more available choice for companies with confined costs or smaller production runs. The low setup prices coupled with minimal product spend donate to an cheaply practical answer, specifically for large or heavy things that could be high priced to produce using different methods.
Rotomolding can also be recognized to be environmentally friendly. The method generates very little spend, as any surplus plastic may frequently be reused. Also, because there are number chemical responses or pressure-related power needs, rotomolding includes a smaller environmental impact compared to other plastic building techniques.

In industries where endurance and stability are vital, rotomolded services and products continually perform. They are often used in challenging situations, including agriculture, water therapy, and construction, wherever weight to UV rays, moisture, and technical wear is essential. With the right material selection, rotomolded items may last for years without dropping performance or appearance.
In conclusion, rotomolding provides a smart, successful, and highly flexible answer for manufacturers seeking quality and performance. From its seamless structure and effective toughness to their charge and design advantages, this method continues to guide creativity across multiple sectors. For firms seeking to produce strong, custom, and trusted plastic products and services, rotomolding remains a respected selection in modern manufacturing.